We spend a day at the Sanand facility that Tata has spent over Rs 2,000 crore in acquiring and retooling to produce the Nexon and Nexon EV.
Published On May 23, 2024 02:00:00 PM
A little more than a year ago, on January 10, 2023, Tata Motors acquired Ford’s factory in Sanand, Gujarat for a significant Rs 725.7 crore, and in that short span of time, the Indian brand has already begun rolling out its Nexon compact SUV – in petrol, diesel and all-electric form – from the plant. In fact, the first petrol and diesel Nexons came off the production line in January this year, while the same line also began producing the Nexon EV from April onwards.
That this assembly line can produce both, ICE (internal combustion engine) models and EVs, and that it can produce a Nexon from start to finish every 16 hours, is a result of Tata’s massive Rs 1,300 crore investment for retooling the Sanand facility. In addition to the Ford hardware that was installed in the plant, Tata added over a 100 more robots and integrated JLR’s software and control units in the facility. Spread across a 460-acre plot of land, the plant currently has an annual production capacity of 3 lakh units, and Tata says that can be scaled up to 4.2 lakh units a year.
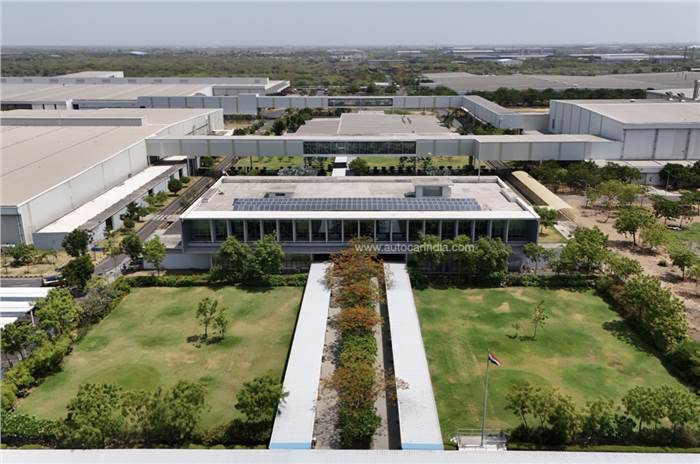
Plant to transition to 100 percent renewable energy by 2026.
Despite the 44-degree Celsius heat, I was excited to get a peek inside what is said to be a state-of-the-art manufacturing facility, and our tour began with the paint shop, though it’s not where the production process begins. It was fascinating to see the Nexon’s entire monocoque being dipped into a vat of grey goo – this electro-static finish is what goes under the primer. It’s only after that that the primer and paint are sprayed on by robotic arms, outside and in. What is interesting is that the company says the Tata Passenger Electric Mobility Plant, Sanand, is among the first in India to have a continuously moving line paint shop line; automation levels are said to be 50 percent. Naturally, the final polishing work is taken up by the factory workers.
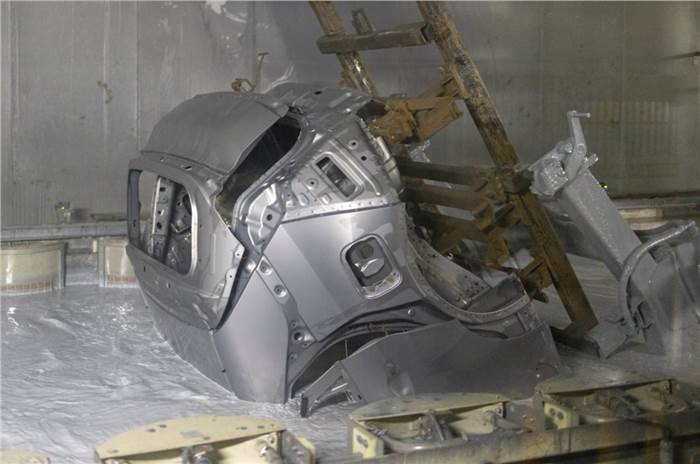
The paint shop incorporates over 80 robots.
However, before the vehicle to be enters the paint shop, the underbody is mated to the doors through automated spot welding machines, and what’s somewhat unique is that none of these large body panels are manually forklifted through the facility. It’s all brought in by automated lifts and robotised arms. The roof is then installed at a separate section, and it’s only after that that the vehicle goes into the paint shop. The weld shop is said to be 98 percent automated (specifically for spot welding), and the level of automation in the press shop is claimed to be at 80 percent.
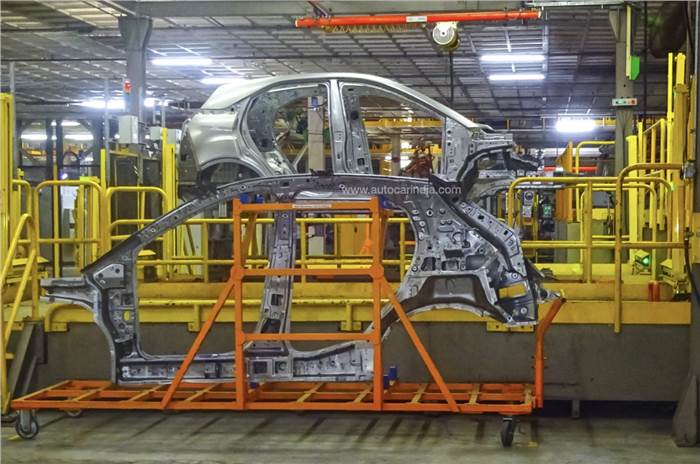
Tata claims the weld shop is 98 percent automated.
Now finished in its final colour (sans the polish), the Nexon is then ferried to the powertrain line, where, as mentioned above, ICE (including CNG) and EV powertrains, along with other mechanical systems like the suspensions and brakes, are bonded to the chassis. Tata Motors has confirmed that the production line is modular in nature, and is capable of producing four different platforms, and up to eight different variants at the same time, without the need for sorting the models into batches – in essence, this means that the brand has the capability to produce the upcoming Curvv, among other models, at the Sanand plant at the same time as the Nexon.
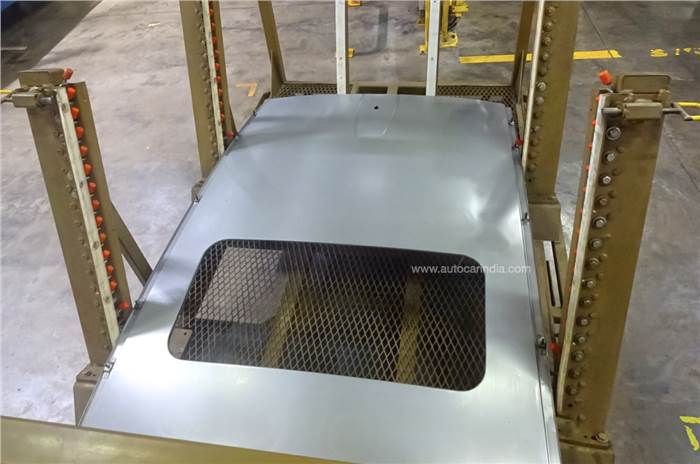
Sunroof-equipped Nexon variants see a little more human input.
As the compact SUV rolls off the final part of the production line, called the TCF (Trim, Chassis, and Final) shop, where, as the name implies, all the variant specific features and trimmings are added, the engine (or electric powertrain) is started for the first time. As the Nexon reaches the end of the conveyor belt, it rolls off under its own power to the final inspection, and that was quite exciting to watch. It then undergoes another systems check for functions like the 360-degree camera. Of course, the Nexons are then taken to the in-house test track to ensure it meets the standards Tata has set for ride and handling.
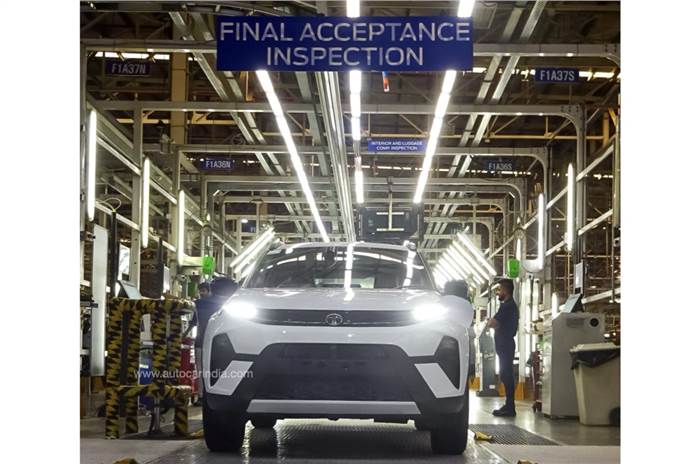
Tata employs over 1,000 workers at the Sanand facility, most of whom were former Ford employees. Beyond the normal level of skill development that carmakers in India hope to instil in their employees, Tata has tied up with Ganpat University to upskill its workers at an in-house facility called Nalanda. The company offer all its Sanand factory workers the opportunity to avail UGC approved diplomas, B. Tech and M. Tech programmes. It’s heartening to see that the brand is not just investing in automation and efficinecy, but also in human capital.
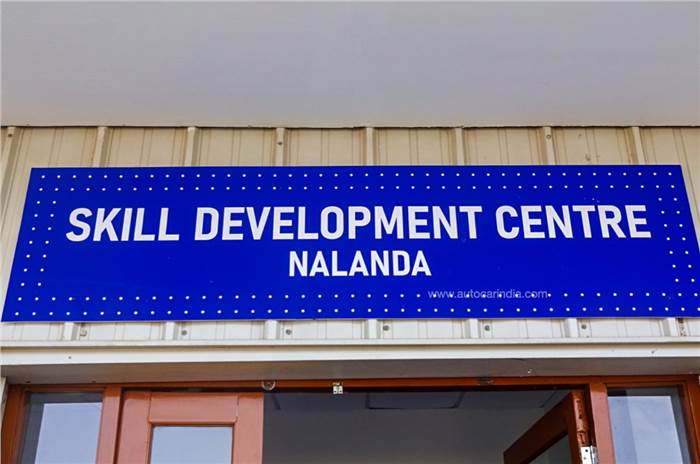
Also see:
Tata Punch EV road test, review
Tata Nexon likely to get panoramic sunroof
Tata Altroz Racer to get unique dual-tone paint scheme
Copyright (c) Autocar India. All rights reserved.